Quelle est l'innovation la plus marquante dans le secteur manufacturier depuis les 20 dernières années?
Dans une perspective de production, «c'est peut-être l'imposition des petites et moyennes entreprises comme moteurs de développement de l'économie et comme créatrices d'emplois», observe Georges Abdul-Nour, professeur en génie industriel à l'Université du Québec à Trois-Rivières et directeur de groupe de recherche à l'Institut de recherche sur les PME.
Plutôt que d'en soutenir seules les coûts, les grandes entreprises ont diffusé dans leur réseau de sous-traitants les efforts de recherche. «Cette structure modulaire a révolutionné la façon de faire des entreprises, soutient le professeur. Aujourd'hui, on est plus flexible, plus agile à envoyer plusieurs modèles sur le marché à une vitesse rapide.»
Cette souplesse permet maintenant de fabriquer plusieurs modèles simultanément sur la même ligne de production, autorisant davantage de déclinaisons pour mieux les adapter aux besoins spécifiques des diverses clientèles.
Sous l'angle des produits manufacturés
Par un autre chemin, le directeur de l'École de design industriel de l'Université de Montréal, Philippe Lalande, pointe lui aussi dans la direction d'une plus grande personnalisation du produit.
«Il n'y a aucun doute pour moi que le prototypage rapide est en train de bouleverser le paysage de la production industrielle», lance-t-il.
Apparus au début des années 2000, ces appareils fabriquent des pièces complexes strate par strate, sans passer par la coûteuse étape de la fabrication de moules - une manière d'impression en trois dimensions. Utile pour la fabrication de prototypes, cette technologie permet également la fabrication personnalisée, en petite série et décentralisée.
«Après 20 ans de croissance, on n'a vu que la toute petite pointe de l'iceberg, soutient Philippe Lalande. Les nouveaux modèles de production «individualisable» changeront nos rapports avec l'objet industriel.»
Plus concrètement, comment l'innovation s'exprime-t-elle dans le secteur manufacturier québécois? En voici six exemples.
1769 : Machine à vapeur, James Watt
1821 : Moteur électrique, Michael Faraday
1876 : Ampoule électrique, Thomas Edison
1885 : Automobile, Karl Benz
1903 : Aéroplane, frères Wright
1913: Chaîne d'assemblage, Henry Ford
1927 : Téléviseur, Philo Taylor Farnsworth
1935 : Nylon, Wallace Carothers
1947: Transistor
1958 : Circuit intégré
1970 : Fibre optique
1979 : Téléphonie cellulaire
1981 : Ordinateur personnel, IBM PC
1990 : Nanotechnologies
1995 : DVD
1997 : Voiture hybride, Toyota Prius
2010 : iPad
2025 : Ordinateur à ADN
Photothérapie par DEL
Les jeunes ingénieurs François Tremblay et Charles-Benoît Germain travaillaient depuis 2002 sur l'utilisation des DEL en serre. S'appuyant sur des études sur l'effet bénéfique de la lumière pour l'humain, les deux fondateurs de Ledma Lab ont conçu un appareil qui baigne son utilisateur dans une lueur colorée.
«On a développé une technologie de lumière qui pénètre la peau à des profondeurs bien précises pour aller stimuler ou inhiber certains mécanismes naturels du corps», décrit François Tremblay.
Sous le dôme qui couvre ce lit, ils ont assemblé 800 DEL à haute puissance de cinq longueurs d'onde différentes, dont la combinaison dosée par ordinateur soulage divers maux comme l'inflammation, l'acné, le psoriasis ou l'eczéma. «On se fie à plus d'une cinquantaine d'études», assure-t-il.
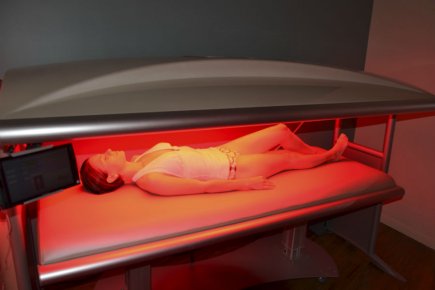
Photo fournie par Ledma Lab
La révolution DEL
Les diodes électroluminescentes (DEL) sont en train de révolutionner l'univers de la lumière artificielle. Le fabricant québécois Lumec a lancé en septembre ses premiers luminaires extérieurs d'ambiance éclairés par DEL, dessinés par Morelli designers.
Les DEL consomment une fraction de l'énergie des lampes standard, et ont une durée de vie nettement supérieure. Il faut toutefois multiplier les diodes pour obtenir une luminosité équivalente. Sur les premiers luminaires d'éclairage routier lancés par Lumec, la lumière de chaque DEL était orientée dans une direction précise par un minuscule prisme, de telle manière que l'ensemble des faisceaux couvre la surface à éclairer.
Sur le nouveau luminaire urbain UrbanScape, chaque DEL est plutôt munie d'un diffuseur en forme d'arachide, qui distribue sa lumière uniformément sur la zone éclairée.
Retenue par quatre fines membrures, la calotte en aluminium est compartimentée d'ailettes soigneusement disposées pour dissiper la chaleur émise par la plaque de 80 DEL. Elle n'envoie aucune lumière vers le ciel, réduisant ainsi la pollution lumineuse nocturne.
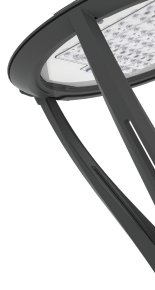
Illustration fournie par LUMEC
Une importante partie de raquette
C'est de la babiche de Formule Un. Le tamis de la raquette Polar Trek de Raquettes GV comporte des empiècements en fibres de carbone encapsulés sur un feuillard de plastique laminé. Le tamis est ainsi plus léger et plus résistant aux déchirures.
C'est la firme Armfoam, de Longueuil, qui a proposé cette technologie unique au manufacturier de Wendake, à laquelle le designer industriel Rino Bourgouin a donné forme.
«Nous mettons seulement la fibre de carbone aux endroits nécessaires pour empêcher la déchirure, explique Rodrigue McDuff, président d'Armfoam. Sans notre technologie, ce n'est pas possible.»
Armfoam se spécialise dans la fabrication en sous-traitance de pièces composites en plastiques alvéolaires, mousses thermoformables et textiles techniques. L'entreprise fabrique elle-même ses machines de production. «On a développé des méthodes assez uniques, qui sont brevetées, affirme Richard Delisle, directeur des ventes. C'est pourquoi, même si vous nous le demandiez, nous vous refuserions l'accès à l'usine.» Zut.
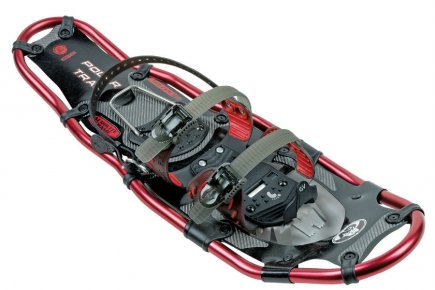
Photo fournie par ARMFOAM
La filière des inventeurs
En 2008, l'idée de Line Quintal et de sa fille Cynthia Bourdeau n'existait que sous la forme d'une courte description: un petit appareil électronique qui ferait sonner un minuscule témoin attaché à un objet que les personnes âgées (ou non) égarent souvent.
Cas rarissime chez les inventeurs: trois ans plus tard, Line Quintal porte au cou la version finale de l'appareil, qui sera mis en marché au début de 2012. La télécommande en forme de huit, de la taille du pouce, est munie de deux boutons disposés dans une arabesque. Elles l'ont elles-mêmes dessinée.
Elles ont confié le développement à diverses firmes qui se sont cassé les dents sur les problèmes de miniaturisation et de radiofréquence: le témoin devait émettre un signal de 80 décibels, avoir une portée de 200 pieds, tout cela dans un format de timbre-poste.
C'est finalement le Centre d'intégration technologique de Sainte-Thérèse qui a réussi la mise au point électronique, tandis que Tak Design se chargeait de la conception des boîtiers.
Et si on égare la télécommande? Elles y ont pensé: l'emballage du Buzz Finder en contient deux. «Le bouton supérieur de la télécommande permet de retrouver l'autre», décrit Line Quintal.
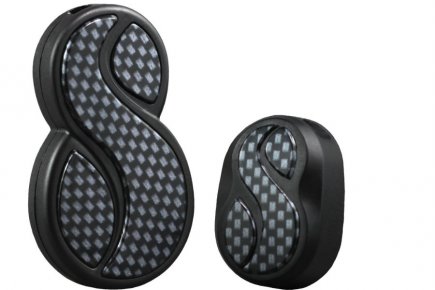
Photo fournie par SOS FINDER
Le mobilier...ultramobile
L'objectif: battre IKEA... sur le terrain où il est absent. Menacé sur son marché de panneaux de fibres (MDF) laqués, Megalak, de Laval, a décidé de créer sa propre marque de meubles à assembler, Nexera. Lancée au début novembre, sa nouvelle collection Allure combine divers modules aux lignes géométriques.
Supprimant toute poignée, le designer industriel Yves Bouchard et son équipe ont creusé dans le chant des panneaux frontaux des gorges suffisamment profondes pour les doigts.
Nexera a mis sur pied un système de livraison à domicile par messagerie partout en Amérique du Nord. «Le défi était d'avoir des emballages excessivement performants et peu coûteux», exprime Yves Bouchard.
La solution: les pièces du meuble sont retenues dans un film thermorétrécissable. Ce bloc compact est muni de pare-chocs en bois à ses deux extrémités, eux-mêmes recouverts d'amortisseurs en mousse de polystyrène. Le tout est glissé dans une boîte de carton ondulé renforcée de cornières sur ses arêtes, et elle aussi pelliculée pour la protéger des intempéries.
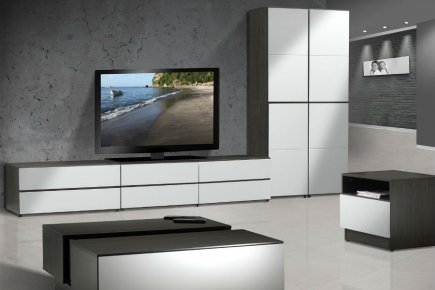
Photo fournie par NEXERA
La puce à l'oreille
La sensation est étrange, mais parfaitement indolore: gonflée par le silicone qui y est lentement injecté, une membrane souple se configure au conduit auditif de chacune des deux oreilles. Le dispositif ressemble à un casque d'écoute, où chaque oreille accueille un système d'injection.
Une gâchette libère un piston à ressort qui pousse et mélange le silicone et son catalyseur. Quatre minutes plus tard, on peut retirer le casque et en détacher des écouteurs qui épousent parfaitement le conduit auditif.
«L'avantage, c'est le confort qu'ils procurent», explique Jean-Nicolas Laperle, président de Sonomax.
Son entreprise se spécialisait dans les embouts auriculaires moulés dans l'oreille, mais chaque moulage devait être effectué par un spécialiste. Avec les Sculpted Eers, chacun peut mouler à la maison ses écouteurs personnels.
Dans une première version, l'injection du silicone et du catalyseur s'effectuait à l'aide d'une petite pompe à levier, en deux étapes successives que l'usager risquait d'intervertir. La production avait à peine commencé que M. Laperle voulait déjà améliorer son produit. La firme de design Brio Innovation a rapidement mis au point le système d'injection contrôlée par ressort, qui a remporté le 8 novembre un prix d'innovation.
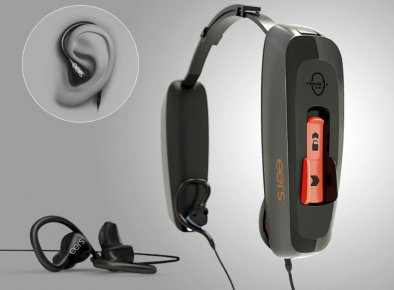
Photo fournie par Brio innovation